Pulley Size and Configuration: The size and configuration of pulleys have a direct impact on the choice of V-ribbed belt and its performance within the automotive engine. Larger pulleys, typically found on components like the crankshaft or water pump, require longer belts to span their circumference adequately. Conversely, smaller pulleys, such as those on ancillary components like air conditioning compressors, demand shorter belts. The number and spacing of grooves on the pulleys must align precisely with the ribs on the belt to prevent slippage and ensure efficient power transfer.
Pulley Material and Surface Finish: Pulleys are commonly manufactured from materials like steel, aluminum, or composite materials. The surface finish of these pulleys is crucial, as it directly affects the friction between the belt and the pulley. A smooth surface finish reduces friction, thereby minimizing wear on both the belt and the pulley. The choice of material influences factors such as weight, durability, and thermal conductivity, all of which impact the overall performance and longevity of the pulley system.
Pulley Alignment: Accurate alignment of pulleys is essential for maintaining proper tension and load distribution along the V-ribbed belt. Misalignment can lead to uneven wear and premature failure of the belt. Achieving precise alignment requires meticulous installation and adjustment of the pulley system, often utilizing specialized tools and techniques to ensure each pulley is positioned correctly relative to the others. Proper alignment is critical for maximizing power transmission efficiency and minimizing maintenance requirements.
Pulley Tensioning Mechanism: The tensioning mechanism in the pulley system is responsible for maintaining the V-ribbed belt at the optimal tension for efficient operation. Automatic tensioners, commonly employed in modern automotive engines, dynamically adjust belt tension to compensate for variations in load, temperature, and belt wear. Manual tensioning systems, on the other hand, allow for periodic adjustment by the user or mechanic to ensure proper tensioning. Proper tensioning is vital for preventing belt slippage, reducing wear, and maximizing the service life of the V-ribbed belt.
Pulley Bearing Arrangement: The arrangement and quality of bearings in the pulley system are critical for ensuring smooth rotation and minimizing friction. High-quality bearings, properly lubricated and sealed, reduce resistance and wear on both the pulleys and the V-ribbed belt. Sealed bearings provide additional protection against contamination and moisture ingress, enhancing durability in harsh operating environments. Regular inspection and maintenance of bearings are essential to detect and address any issues promptly, preventing costly downtime and potential damage to the pulley system.
Pulley Misalignment Correction: Some modern pulley systems feature built-in mechanisms to automatically correct misalignments caused by factors such as engine vibrations, component wear, or belt stretching. These self-adjusting features help maintain optimal belt tension and alignment, reducing the risk of premature wear and failure. Additionally, proactive maintenance practices, such as periodic alignment checks and belt tension adjustments, can help identify and rectify alignment issues before they escalate into more significant problems. By integrating misalignment correction mechanisms into the design of the pulley system, automotive engineers can enhance overall reliability and performance, ultimately improving the longevity and efficiency of V-ribbed belts in automotive applications.
Automotive V-Ribbed Belts
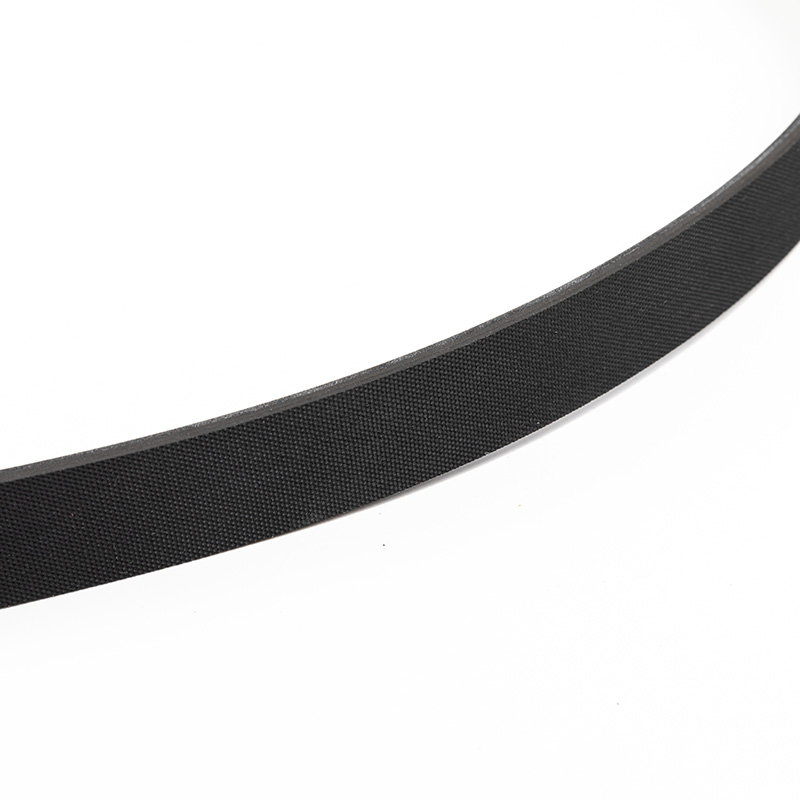